导语
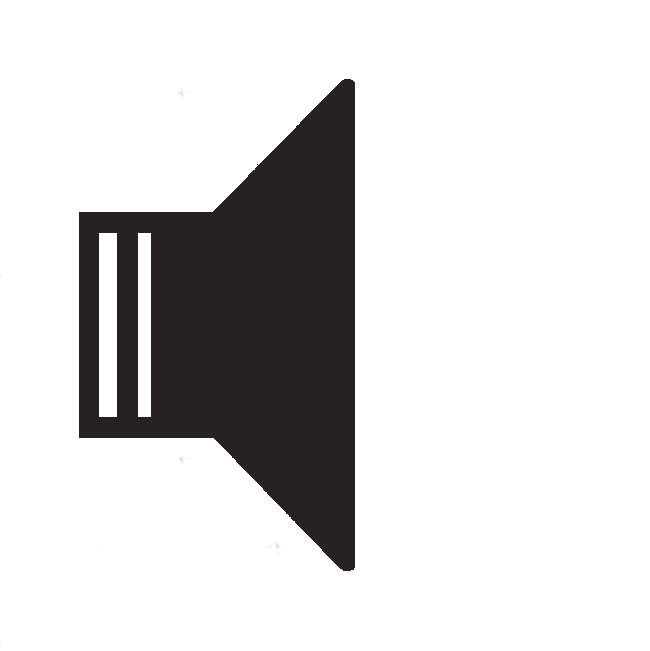
内容提要
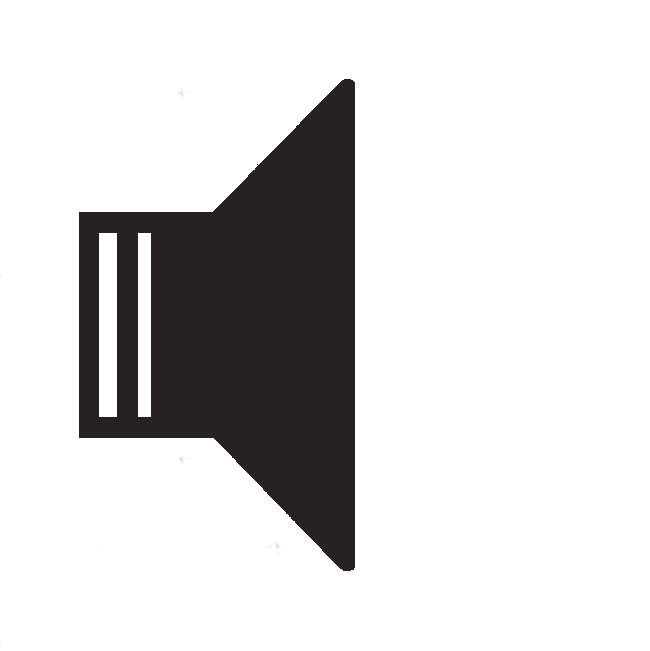
本书以机械产品常用金属材料为重点,介绍了各类金属材料的基本知识、成分和性能特点及影响因素,以及保证和提高材料使用功能的生产、加工、热处理、表面处理等内容;根据对典型零件的功能分析和材料在不同工况条件下的使用特征,说明了材料选择和应用原则;结合典型零件失效分析,讨论了失效原因和应采取的对策。
书后以附录形式为读者提供了金属材料方面常用数据资料。
本书可供机械产品设计或制造单位的设计、工艺、热处理及材料采购、检验、质量控制等各类人员使用,也可作为科研单位和工科院校金属材料、机械设计、机械加工等专业教师、学生的参考资料。
目录
第1章 金属材料的相关知识
1.1 概述
1.2 金属材料的晶体结构
1.2.1 空间点阵和晶格
1.2.2 晶胞
1.2.3 晶系
1.2.4 常用金属结构类型
1.2.5 实际金属晶体结构的特点
1.3 金属的同素异晶转变
1.4 铁碳合金中的基本组织
1.4.1 铁素体
1.4.2 奥氏体
1.4.3 渗碳体
1.4.4 珠光体
1.4.5 莱氏体
1.4.6 贝氏体
1.4.7 马氏体
1.4.8 索氏体
1.4.9 托氏体(屈氏体)
1.5 铁碳合金状态图(相图)
1.5.1 铁碳合金状态图
1.5.2 合金元素对铁碳合金状态图的影响
1.6 钢的结晶和固态相变
1.6.1 共析钢
1.6.2 亚共析钢
1.6.3 过共析钢
1.7 钢的过冷奥氏体转变曲线图及应用
1.7.1 钢的等温转变及奥氏体等温转变曲线(TTT曲线)
1.7.2 钢的连续转变及奥氏体连续转变曲线(CCT曲线)
1.7.3 合金元素对过冷奥氏体转变曲线的影响
1.8 钢中合金元素的作用
1.8.1 硅(Si)
1.8.2 锰(Mn)
1.8.3 磷(P)
1.8.4 硫(S)
1.8.5 铬(Cr)
1.8.6 镍(Ni)
1.8.7 钼(Mo)
1.8.8 钒(V)
1.8.9 钛(Ti)
1.8.10 铌(Nb)
1.8.11 钨(W)
1.8.12 铝(Al)
1.8.13 铜(Cu)
1.8.14 硼(B)
1.8.15 钴(Co)
1.8.16 稀土元素(RE)
1.8.17 氮(N)
1.8.18 氢(H)
1.8.19 氧(O)
第2章 金属材料的分类、编号、识别及主要特性
2.1 金属材料的分类
2.1.1 纯金属
2.1.2 合金
2.1.3 黑色金属及合金
2.1.4 有色金属及合金
2.2 钢铁材料牌号表示方法
2.2.1 中国钢铁材料牌号表示方法(GB)
2.2.2 日本钢铁材料牌号表示方法(JIS)
2.2.3 韩国钢铁材料牌号表示方法(KS)
2.2.4 俄罗斯钢铁材料牌号表示方法(ГОСТ)
2.2.5 美国钢铁材料牌号表示方法(SAE、AISI、ASTM、UNS、ASI)
2.2.6 德国钢铁材料牌号表示方法(DIN)
2.2.7 英国钢铁材料牌号表示方法(BS)
2.2.8 法国钢铁材料牌号表示方法(NF)
2.2.9 瑞典钢铁材料牌号表示方法(SS)
2.2.10 欧洲标准钢铁材料牌号表示方法(EN)
2.2.11 国际标准化组织钢铁材料牌号表示方法(ISO)
2.2.12 核泵常用钢铁材料牌号表示方法
2.2.13 钢铁材料的商业牌号
2.3 有色金属及合金牌号表示方法
2.3.1 中国有色金属及合金牌号表示方法(GB)
2.3.2 日本有色金属及合金牌号表示方法(JIS)
2.3.3 俄罗斯有色金属及合金牌号表示方法(ГОСТ)
2.3.4 美国有色金属及合金牌号表示方法(ASTM)
2.3.5 德国有色金属及合金牌号表示方法(DIN)
2.3.6 英国有色金属及合金牌号表示方法(BS)
2.3.7 法国有色金属及合金牌号表示方法(NF)
2.3.8 国际标准化组织有色金属及合金牌号表示方法(ISO)
2.3.9 欧洲标准化委员会有色金属及合金牌号表示方法(EN)
2.4 常用金属材料的特性及用途
2.4.1 普通碳素结构钢
2.4.2 低合金高强度钢
2.4.3 优质碳素结构钢
2.4.4 合金结构钢
2.4.5 弹簧钢
2.4.6 不锈钢
2.4.7 耐热钢
2.4.8 铸钢
2.4.9 非调质钢
2.4.10 灰铸铁
2.4.11 球墨铸铁
2.4.12 可锻铸铁
2.4.13 耐蚀铸铁
2.4.14 抗磨铸铁(含高铬铸铁)
2.4.15 铜及铜合金
2.4.16 铸造铝合金
2.4.17 钛及钛合金
2.4.18 铸造轴承合金
2.4.19 耐蚀合金(高镍合金)
2.4.20 高温合金
2.5 耐磨用金属材料
2.5.1 耐磨铸铁
2.5.2 耐磨合金钢
2.5.3 锰系耐磨钢
2.6 低温用金属材料
2.6.1 低温用钢
2.6.2 钛及钛合金
2.6.3 铝及铝合金
2.6.4 镍基合金
2.7 高温用金属材料
2.8 耐腐蚀用金属材料
第3章 金属材料的成形知识
3.1 炼钢
3.1.1 常见的炼钢方法
3.1.2 钢冶炼时可能产生的质量缺陷及危害
3.2 铸锭(模铸)
3.2.1 铸锭工艺方法
3.2.2 铸锭时可能产生的质量缺陷和危害
3.3 连铸
3.3.1 连铸生产特点
3.3.2 连铸可能产生的质量缺陷及危害
3.4 锻造(锻压)
3.4.1 锻造(锻压)工艺方法
3.4.2 热锻造(锻压)加工可能产生的质量缺陷及危害
3.4.3 锻后热处理
3.5 轧制
3.5.1 轧制加工工艺方法
3.5.2 轧制可能产生的质量缺陷及危害
3.6 拉拔
3.6.1 拉拔加工工艺方法
3.6.2 拉拔可能产生的质量缺陷及危害
3.7 挤压
3.7.1 挤压加工工艺方法
3.7.2 挤压可能产生的质量缺陷及危害
3.8 冲压
3.8.1 冲压加工工艺方法
3.8.2 冲压可能产生的质量缺陷及危害
3.9 铸造
3.9.1 铸造生产的主要工艺方法分类
3.9.2 铸造产品的质量及影响因素
3.10 锻件生产及质量控制
3.10.1 锻件生产流程
3.10.2 锻件质量缺陷及检验
3.10.3 锻件的质量控制
3.11 板材生产及质量控制
3.11.1 板材生产流程
3.11.2 轧板质量缺陷和检验
3.11.3 轧板的质量控制
3.12 管材生产及质量控制
3.12.1 管材生产流程
3.12.2 管材的质量缺陷和检验
3.12.3 钢管的质量控制
3.13 铸件生产及质量控制
3.13.1 砂型铸造铸件生产流程
3.13.2 铸件可能产生的缺陷和检验
3.13.3 铸件的质量控制
第4章 金属材料的性能及影响因素
4.1 金属材料的力学性能及影响因素
4.1.1 金属材料的强度
4.1.2 金属材料的塑性
4.1.3 金属材料的韧性
4.1.4 金属材料的断裂韧性
4.1.5 金属材料的疲劳性能
4.1.6 金属材料的耐磨性能
4.1.7 金属材料的高温性能
4.1.8 金属材料的低温性能
4.1.9 金属材料的硬度
4.2 金属材料的耐腐蚀性能及影响因素
4.2.1 腐蚀的基本知识
4.2.2 金属的钝化
4.2.3 机械零件(产品)常见腐蚀类型
4.2.4 均匀腐蚀
4.2.5 电偶腐蚀
4.2.6 晶间腐蚀
4.2.7 点腐蚀
4.2.8 缝隙腐蚀
4.2.9 应力腐蚀断裂
4.2.10 腐蚀疲劳
4.2.11 空泡腐蚀(腐蚀介质中的气蚀)
4.2.12 冲刷腐蚀和腐蚀磨损
4.3 金属材料的抗辐照性能
4.3.1 辐照效应的结果
4.3.2 影响材料抗辐照性能的材料因素
4.4 金属材料的物理性能
4.4.1 比热容
4.4.2 热膨胀性
4.4.3 导热性
4.4.4 热稳定性
4.4.5 密度
4.4.6 熔点
4.4.7 电阻
4.4.8 弹性模量
4.4.9 切变模量
4.4.10 泊松比
4.5 金属材料的工艺性能
4.5.1 铸造性能(可铸性)
4.5.2 锻压性能(可锻压性)
4.5.3 焊接性能(可焊性)
4.5.4 切削加工性能(可切削性)
4.5.5 热处理性能(可热处理性)
第5章 金属材料的热处理
5.1 钢的热处理原理
5.1.1 钢加热(保温)过程的转变
5.1.2 奥氏体冷却过程的转变
5.1.3 钢回火时的转变
5.1.4 钢的时效强化
5.2 钢常见的热处理方法
5.2.1 钢的均匀化退火
5.2.2 钢的完全退火
5.2.3 钢的不完全退火
5.2.4 钢的等温退火
5.2.5 钢的去应力退火
5.2.6 钢的正火
5.2.7 钢的淬火
5.2.8 钢的回火
5.2.9 钢的调质处理
5.2.10 钢的冷处理
5.2.11 钢的固溶处理
5.2.12 钢的时效(沉淀硬化)处理
5.2.13 钢的调整处理
5.2.14 钢的稳定化退火处理
5.2.15 不锈钢的敏化处理
5.2.16 钢的火焰表面淬火
5.2.17 钢的感应加热表面淬火
5.2.18 钢的激光表面淬火
5.2.19 钢的真空热处理
5.2.20 钢的可控气氛热处理
5.2.21 钢的渗碳
5.2.22 钢的渗氮
5.2.23 钢的碳氮共渗
5.2.24 钢的氮碳共渗
5.2.25 钢的硫氮碳共渗
5.2.26 钢的QPQ处理
5.2.27 钢的渗硼
5.2.28 钢的渗金属
5.3 典型金属材料的热处理
5.3.1 调质钢的热处理
5.3.2 弹簧钢的热处理
5.3.3 工具类钢的热处理
5.3.4 轴承钢的热处理
5.3.5 马氏体时效钢的热处理
5.3.6 铁素体不锈钢的热处理
5.3.7 奥氏体不锈钢的热处理
5.3.8 奥氏体-铁素体双相不锈钢的热处理
5.3.9 马氏体不锈钢的热处理
5.3.10 沉淀硬化不锈钢的热处理
5.3.11 耐热钢的热处理
5.3.12 高温合金的热处理
5.3.13 耐蚀合金的热处理
5.3.14 低温用钢的热处理
5.3.15 灰铸铁的热处理
5.3.16 球墨铸铁的热处理
5.3.17 高铬白口抗磨铸铁的热处理
5.3.18 铜及常用铜合金的热处理
5.3.19 铝及铝合金的热处理
5.3.20 钛及钛合金的热处理
第6章 金属材料的表面处理
6.1 堆焊
6.1.1 堆焊材料
6.1.2 堆焊方法
6.1.3 堆焊的质量检验和质量控制
6.2 热喷涂
6.2.1 热喷涂原理概述
6.2.2 热喷涂材料
6.2.3 热喷涂方法、种类及特点
6.2.4 热喷涂层的选用原则
6.2.5 待喷涂面的制备
6.2.6 热喷涂层的质量检验和质量控制
6.3 电镀
6.3.1 电镀的基本知识
6.3.2 电镀层的分类
6.3.3 电镀方法的标志(用于紧固件)
6.3.4 镀前的表面处理
6.3.5 镀后处理
6.3.6 电镀层的质量检验和质量控制
6.4 镀硬铬
6.4.1 镀铬层特性
6.4.2 镀硬铬的工艺程序及控制
6.4.3 镀铬层的质量检验和质量控制
6.4.4 核电产品的镀铬
6.4.5 镀硬铬对疲劳强度的影响
6.4.6 对于其他金属和合金镀层的相关说明
6.5 化学镀
6.5.1 化学镀的机理及特点
6.5.2 化学镀镍用材料
6.5.3 化学镀镍层的性能特点及应用
6.5.4 化学镀层的质量检验和质量控制
6.6 磷化
6.6.1 磷化及其作用
6.6.2 磷化液配方的选择
6.6.3 磷化处理工艺要点
6.6.4 磷化层的质量检验和质量控制
6.6.5 磷化工艺的工序安排
6.7 发蓝
6.7.1 发蓝处理及其作用
6.7.2 发蓝溶液的配方及其反应机理
6.7.3 发蓝的工艺流程及控制要点
6.7.4 发蓝的质量检验
6.7.5 低温和常温发蓝(黑)工艺
6.7.6 发蓝工艺的工序安排
6.8 其他表面处理新技术介绍
6.8.1 气相沉积技术
6.8.2 高能束技术(激光合金化技术和离子注入技术)
6.9 表面处理的正确选择和实施
6.9.1 表面处理类型的正确选择
6.9.2 表面处理工艺的正确实施
第7章 金属材料的检验与试验
Ⅰ化学成分检验
7.1 金属材料的化学成分检验
7.1.1 常见的分析检验方法
7.1.2 取样和制样
7.1.3 检验分析
7.1.4 结果评定和允许偏差
Ⅱ力学性能检验
7.2 金属材料的硬度试验
7.2.1 布氏硬度试验
7.2.2 锤击式布氏硬度试验
7.2.3 洛氏硬度试验
7.2.4 维氏硬度试验
7.2.5 肖氏硬度试验
7.2.6 里氏硬度试验
7.2.7 钢铁硬度与强度的换算关系
7.3 室温拉伸试验
7.3.1 静拉伸试验原理
7.3.2 试验设备要求
7.3.3 拉伸试样制备
7.3.4 拉伸试验的一般要求及结果评定
7.4 高温拉伸试验和低温拉伸试验
7.5 室温冲击试验
7.5.1 冲击试验原理
7.5.2 试验设备要求
7.5.3 冲击试样制备
7.5.4 冲击试验的一般要求和结果评定
7.6 高温冲击试验和低温冲击试验
7.7 金属材料的磨损试验
7.7.1 典型的磨损试验机
7.7.2 磨损结果的测定及表示方法
7.8 力学性能的其他试验方法
7.8.1 疲劳试验
7.8.2 压缩试验
7.8.3 静扭转试验
7.8.4 剪切试验
7.8.5 落锤试验和动态撕裂试验
7.8.6 断裂韧度试验
7.8.7 高温强度试验
Ⅲ工艺性能试验
7.9 金属管的扩口试验和压扁试验
7.9.1 金属管的扩口试验
7.9.2 金属管的压扁试验
Ⅳ腐蚀试验
7.10 均匀(全面)腐蚀试验
7.11 不锈钢的晶间腐蚀试验
7.12 不锈钢三氯化铁点腐蚀试验
7.13 腐蚀试验的其他方法
7.13.1 盐雾腐蚀试验
7.13.2 不锈钢缝隙腐蚀试验
7.13.3 不锈钢应力腐蚀试验
7.13.4 电偶腐蚀试验
7.13.5 点腐蚀电位测量试验
7.13.6 点腐蚀临界温度试验
7.13.7 腐蚀疲劳试验
7.13.8 空泡腐蚀试验
7.13.9 腐蚀磨损试验
Ⅴ无损检验(检测)
7.14 渗透检测(PT)
7.15 磁粉检测(MT)
7.16 超声波检测(UT)
7.17 射线检测(RT)
7.18 涡流检测(ET)
7.19 无损检测的其他方法
7.19.1 声发射检测(AE)
7.19.2 光纤检测
7.19.3 红外线检测(IT)
Ⅵ宏观组织缺陷检验
7.20 钢材的酸蚀检验
7.21 钢材的硫印检验
7.22 宏观检验的其他方法
Ⅶ显微组织检验
7.23 金属基本组织的检验与评定
7.23.1 钢的基本组织检验和评定
7.23.2 铸铁的基本组织检验与评定
7.23.3 有色金属及合金的组织检验
7.24 钢中非金属夹杂物的检验与评定
7.25 带状组织和魏氏组织的检验与评定
7.25.1 带状组织的检验与评定
7.25.2 魏氏组织的检验与评定
7.26 奥氏体不锈钢和奥氏体-铁素体双相不锈钢中α相的检验与评定
7.27 钢的脱碳层深度的检验与评定
7.28 钢的渗氮层的检验与评定
7.29 金属平均晶粒度的检验与评定
7.30 金属表面硬化层深度的检验与评定
第8章 材料的采购与验收
8.1 材料采购技术规格书(技术条件)
8.2 供货商的考察、评定和资格认定
8.3 材料(铸、锻件)生产过程中的质量监控
8.4 采购材料的复验和验收
8.5 材料代用
第9章 产品设计的材料选择
9.1 以力学性能为主的零件选材
9.2 摩擦磨损条件下零件选材
9.2.1 黏着磨损及选材
9.2.2 减摩材料的选用
9.2.3 磨料磨损、冲蚀磨损及选材
9.2.4 汽蚀及选材
9.3 低温条件下的零件选材
9.4 高温条件下的零件选材
9.5 腐蚀条件下零件选材
9.5.1 腐蚀介质及腐蚀
9.5.2 影响腐蚀的因素
9.5.3 金属材料的耐蚀性
9.5.4 腐蚀选材
9.6 核电设备对金属材料的特殊要求
9.6.1 核环境的特殊性
9.6.2 核电设备的选材
第10章 典型零件选材、工序质量控制分析和典型零件失效分析
10.1 典型零件选材和工序质量控制分析
10.1.1 主给水泵泵轴
10.1.2 耐腐蚀泵泵轴
10.1.3 海水提升泵叶轮
10.1.4 潜卤泵叶轮
10.1.5 渣浆泵叶轮
10.1.6 锅炉给水泵筒体
10.1.7 飞轮
10.1.8 轴套
10.1.9 平衡套
10.1.10 多级泵拉紧螺栓
10.1.11 给水泵主螺栓
10.1.12 双头螺栓
10.1.13 主螺母
10.1.14 弹簧
10.1.15 耐腐蚀泵壳体
10.1.16 轴承套圈
10.2 因选材或处理不当引起的零件失效分析
10.2.1 轴断裂失效分析(一)
10.2.2 轴断裂失效分析(二)
10.2.3 泵轴脆断失效隐患分析
10.2.4 叶轮磨蚀失效分析(一)
10.2.5 叶轮磨蚀失效分析(二)
10.2.6 紧固螺栓松弛失效分析
10.2.7 不锈钢螺柱锈蚀失效分析
10.2.8 螺母裂纹失效分析
10.2.9 泵轮叶片裂纹失效分析
10.2.10 涡轮套裂纹失效分析
10.2.11 输水管应力腐蚀破裂失效分析
10.2.12 试验回路管路穿孔失效分析
附录
附录A 缩写
A1标准相关缩写
A2材料相关缩写
A3熔炼及铸造相关缩写
A4锻压加工相关缩写
A5热处理及表面(改性)处理相关缩写
A6焊接相关缩写
A7性能相关缩写
A8组织分析相关缩写
A9无损检测相关缩写
A10腐蚀相关缩写
附录B 术语
B1金属材料术语
B2金属熔炼术语
B3铸造术语
B4锻压加工术语
B5焊接术语
B6金属热处理术语
B7力学性能术语
B8无损检测术语
B9金属腐蚀术语
附录C 常用数据、资料
C1元素的物理化学性质
C2常用不锈钢材料物理化学性质
C3常用有色金属材料的密度
C4温度换算(摄氏度华氏度)
C5黑色金属各种硬度之间的换算
C6肖氏硬度与洛氏、布氏、维氏硬度的换算
C7里氏硬度换算
C8钢铁硬度与强度换算表(一)
C9钢铁硬度与强度换算表(二)
C10力学性能新旧名称对照表
C11不同腐蚀速率单位的换算系数
C12铸铁常用的浸蚀剂
C13结构钢与工具钢常用的侵蚀剂
C14不锈钢常用腐蚀试剂
C15常用电解抛光液的配方、适用范围及工作参数
C16渗层组织常用侵蚀试剂
C17常用钢材理论质量的计算方法
C18钢材的涂色标记
参考文献